Exploring the Benefits and Innovations of a CNC Turn Parts Factory
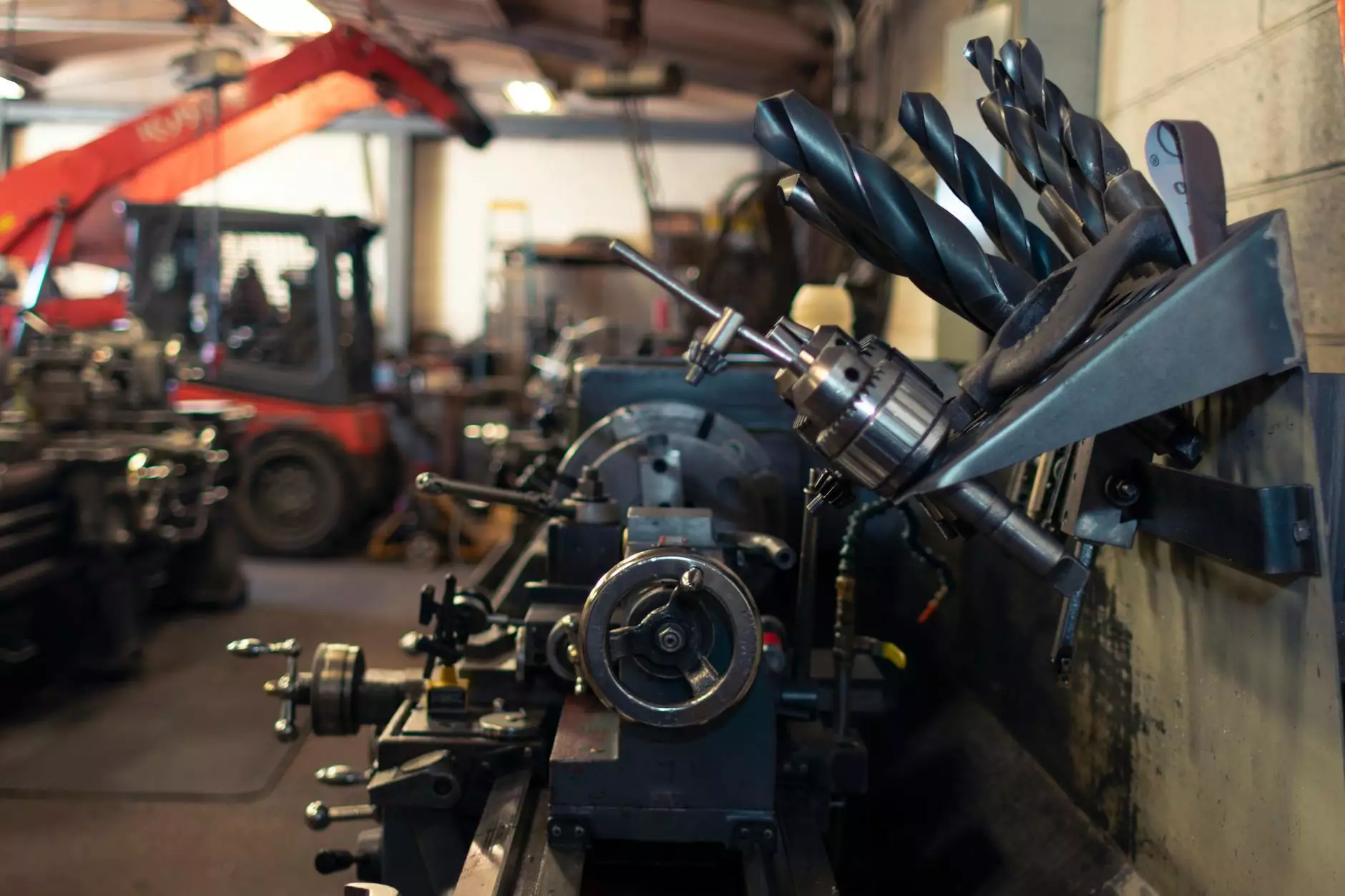
A cnc turn parts factory is at the forefront of modern manufacturing, especially in the realm of metal fabrication. With the rise of technology and automation, these factories play a critical role in producing intricate parts with unparalleled accuracy. This article will explore the numerous advantages of using a CNC turn parts factory, its impact on the metal fabricators industry, and the technological innovations leading the charge in this sector.
What is a CNC Turn Parts Factory?
A CNC (Computer Numerical Control) turn parts factory employs computerized technology to control the movement of machinery and tools used in machining processes. These factories specialize in turning operations, where raw materials, typically metal, are shaped by a cutting tool revolving around a fixed axis. The precision and efficiency of CNC machining allow for the production of complex shapes and components, which are essential in a variety of industries, including automotive, aerospace, and electronics.
The Advantages of CNC Turn Parts Manufacturing
1. Enhanced Precision and Accuracy
CNC turning processes are renowned for their high precision. The ability of CNC machines to repeat the same operation with unwavering accuracy ensures that each part produced meets stringent quality standards. This level of precision is paramount in sectors where tolerances can be as tight as a few microns, ensuring components fit perfectly within larger assemblies.
2. Increased Production Efficiency
In a cnc turn parts factory, production efficiency is significantly enhanced. CNC machines can operate continuously, allowing for 24/7 production cycles with minimal human intervention. This continuous operation not only accelerates manufacturing but also reduces labor costs and the likelihood of human error, which can lead to defects.
3. Flexibility in Design and Production
One of the standout features of CNC turning is its flexibility. Designers can easily adapt designs and modifications without requiring extensive retooling. This capability allows manufacturers to quickly respond to market changes or customer requests, keeping them competitive in a fast-paced industry.
4. Material Versatility
Factories that specialize in CNC turning can work with a wide range of materials including, but not limited to:
- Aluminum
- Stainless Steel
- Brass
- Copper
- Plastics
This versatility enables manufacturers to cater to various industries and project requirements while maintaining quality and precision.
5. Streamlined Quality Control
CNC turning machinery comes equipped with advanced monitoring systems that enable real-time inspections and quality checks. Such systems help in identifying defects or inconsistencies early in the production process, ensuring that the final products meet the highest quality standards.
Technological Innovations in CNC Turning
1. Advanced Software Solutions
Innovations in CNC programming software have transformed the industry. Programs equipped with advanced algorithms can optimize the cutting paths and tool engagements, leading to reduced cycle times and increased tool life. The integration of CAD/CAM software allows for seamless transitions from design to production, further enhancing operational efficiency.
2. Automation and Robotics
Robotic arms and automated loading systems have become common in modern cnc turn parts factories. These technologies minimize the need for manual handling, reduce labor costs, and enhance safety by limiting human interaction with heavy machinery. The result is a more streamlined and efficient manufacturing environment.
3. Additive Manufacturing Integration
One of the emerging trends is the integration of CNC turning with additive manufacturing (3D printing). This combination allows for the rapid prototyping of parts, which can then be precisely finished using CNC techniques. Such a hybrid approach not only saves time but also increases the potential for creating complex geometries that were previously not possible.
Impact on the Metal Fabricators Industry
The introduction of CNC turn parts factories has had a profound impact on the metal fabricators industry. Here are a few noteworthy effects:
1. Cost Efficiency
With increased automation and precision, operational costs have decreased significantly. Manufacturers can produce larger quantities of parts in shorter times, lowering the overall cost per item. This cost efficiency is vital for businesses trying to maintain a competitive edge.
2. Improved Lead Times
As production processes streamline, lead times for manufacturing and delivery of parts have also improved. Clients can expect shorter turnaround times, which is particularly beneficial in industries where rapid response to market demands is critical, such as automotive or electronics.
3. Greater Customization Options
The demand for customized solutions is rising, and CNC turning enables manufacturers to accommodate this need effectively. The ability to program and reprogram machines means that factories can produce unique, customer-specific parts at scale without sacrificing quality.
Conclusion
In conclusion, a cnc turn parts factory represents the pinnacle of innovation in the metal fabrication industry. With the advantages of precision, efficiency, flexibility, and streamlined production processes, these factories are revolutionizing how components are manufactured. As technology continues to advance, the possibilities for CNC turning will only expand, enabling manufacturers to meet the growing demands of various industries while enhancing their operational capabilities. The future of metal fabrication is bright, and CNC turning will undoubtedly play a pivotal role in shaping that future.
For businesses in the metal fabrication sector, partnering with a leading CNC turn parts factory like Deepmould can unlock new opportunities for growth and innovation. Embrace the power of CNC technology and position your business for success!