The Ultimate Guide to Wire Labler Solutions for Your Packaging Needs
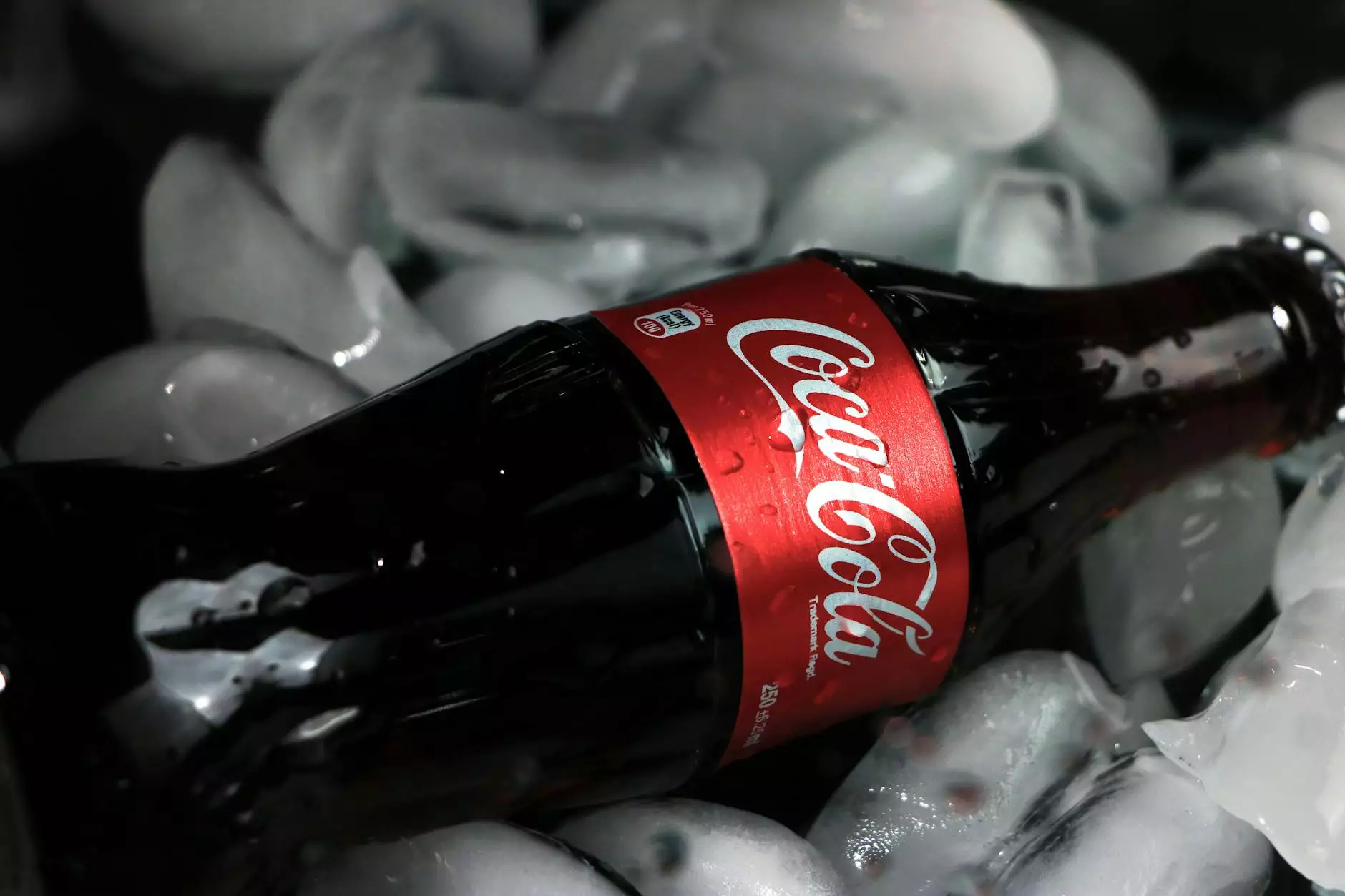
Packaging is a fundamental aspect of product presentation and preservation in various industries. Among the myriad of technologies that aid in packaging efficiency, the wire labler stands out as a crucial device for many businesses. This article provides an in-depth analysis of wire lablers, their functionalities, benefits, and how they impact the packaging equipment landscape, with particular reference to Shineben.com.
What is a Wire Labler?
A wire labler is a specialized tool designed to apply labels to products swiftly and accurately. It is primarily used in industries where products need to be tagged for identification, stocking, or regulatory compliance. These devices can range from manual tools to sophisticated automated systems, depending on production scale and requirements.
Types of Wire Lablers
Wire lablers come in various forms, each suited for different applications. The most common types include:
- Manual Wire Lablers: These are often used in smaller operations where the volume of labeling does not justify a fully automated system.
- Semi-Automatic Wire Lablers: These machines require some manual intervention but increase speed and accuracy compared to manual options.
- Fully Automatic Wire Lablers: Ideal for large-scale operations, these machines operate independently to label products at high speeds.
The Importance of Wire Lablers in Business
Efficiency in labeling is vital for maintaining workflow and productivity in any manufacturing environment. Here are several ways that a wire labler enhances business operations:
1. Improved Efficiency and Productivity
Implementing a wire labler allows businesses to streamline their labeling processes. Automated systems can label hundreds of products per minute, drastically reducing the time spent on manual labeling tasks. This efficiency translates into higher productivity rates, enabling employees to focus on more critical aspects of production.
2. Enhanced Accuracy and Consistency
Human error is an ever-present risk in manual labeling processes. A wire labler minimizes this risk, ensuring that labels are applied consistently and accurately every time. This reliability is crucial for compliance with safety regulations and for reducing the potential for costly mistakes.
3. Cost-Effectiveness
While there is an initial investment involved in purchasing a labeling machine, the long-term savings derived from reduced labor costs and improved operational efficiency can be substantial. Businesses can significantly lower their overhead by increasing the speed and accuracy of their packaging processes.
4. Flexibility in Labeling Options
Modern wire lablers offer a variety of labeling options, allowing businesses to adapt to different product types and sizes. Whether you need to label bottles, boxes, or wires, a quality labler can adjust to meet your packaging needs creatively.
5. Enhanced Product Presentation
Labels are not just functional; they also play a crucial role in product marketing. A well-designed label can attract consumers and convey vital information about the product. Using a wire labler ensures that your labels are affixed neatly, reinforcing the quality perception of your brand.
Implementing Wire Lablers in Your Business
Choosing the right wire labler for your specific needs involves several considerations. Here are some tips on successfully implementing a wire labeling solution into your business:
1. Assess Your Labeling Needs
Before investing in a wire labler, assess the volume of products you plan to label and the complexity of your labeling requirements. Understanding the scale of your operations will help determine whether a manual, semi-automatic, or fully operational system is best for your business.
2. Evaluate Your Budget
Budget constraints are a reality for many businesses. When evaluating wire labler options, consider both the upfront cost and the long-term operational savings that such an investment can yield.
3. Research Reliable Manufacturers
When it comes to purchasing packaging equipment, reliability is paramount. Look for reputable manufacturers, like Shineben.com, that provide quality machinery and good customer support. Investing in trustworthy equipment will ensure smooth operations and reduce downtime.
4. Consider Integration with Existing Systems
If your business already has a system in place, consider how a wire labler will integrate into your existing operations. Compatibility can save time and minimize disruptions caused by training staff on new systems.
5. Training and Maintenance
Finally, ensure that your staff is trained to utilize the new equipment effectively. Regular maintenance is also crucial to keep the wire labler functioning optimally, thereby extending its lifespan and ensuring consistent performance.
Conclusion
In the modern fast-paced business environment, the efficiency of operations directly influences profitability. A reliable wire labler from a quality manufacturer like Shineben.com can significantly enhance your packaging process, leading to better productivity, accuracy, and cost savings. Making the right choice in labeling equipment is an investment in the future of your business.
Frequently Asked Questions (FAQs)
1. Can wire lablers be used for all types of products?
While wire lablers are versatile, their effectiveness can depend on the size, shape, and materials of the products. It's essential to choose a labler designed for your specific product types.
2. How often should wire lablers be maintained?
Regular maintenance schedules can vary. However, it's generally recommended to conduct maintenance checks at least once a month or more frequently depending on the volume of use.
3. What are the common issues encountered with wire lablers?
Common issues may include jammed labels, misalignment, or operational failure. Training and regular maintenance can often minimize these risks.
4. Are there options for custom labels?
Yes, many modern wire lablers allow for custom labels, which can help in branding and marketing efforts. Ensure the machine you choose supports the specifications you require.
5. Is training necessary for using a wire labler?
Yes, training is crucial as it ensures that operators can maximize the efficiency of the equipment and prevent operational errors.