Understanding the Role of a **Die Casting Tool Manufacturer**
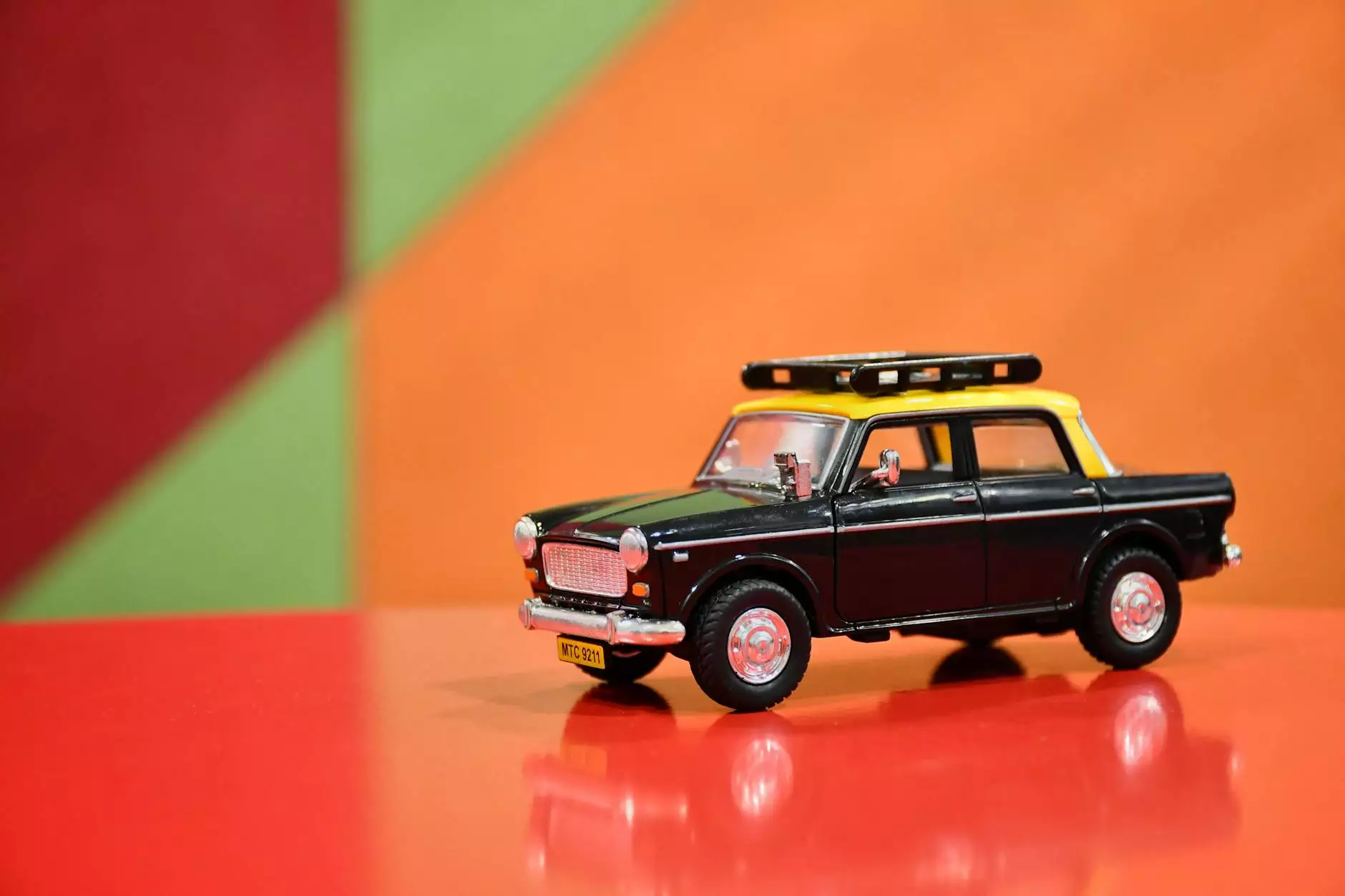
In the realm of manufacturing, die casting has emerged as a pivotal technique, particularly for producing complex shapes and components. As industries evolve and the demand for precision and efficiency increases, the significance of a qualified die casting tool manufacturer becomes more pronounced. This article delves deep into die casting, the manufacturing process involved, and why partnering with a reputable tool manufacturer like DeepMould is essential for any business in want of high-quality metal components.
What is Die Casting?
Die casting is a manufacturing process that involves forcing molten metal under high pressure into a mold (or die). The die is a steel tool that is carefully engineered to form the desired shape of the final product. This technique is widely used in industries such as automotive, electronics, and construction, given its ability to produce parts with high accuracy and minimal post-processing.
The Advantages of Die Casting
- High Precision: The die casting process offers exceptional dimensional accuracy, making it ideal for applications requiring tight tolerances.
- Speed: Once the die is made, the production cycle is rapid, enabling manufacturers to produce large volumes of parts quickly.
- Complex Designs: Die casting allows for the creation of intricate shapes that can often be challenging to produce with other methods.
- Cost-Effectiveness: High production rates can lead to lower costs per unit, especially beneficial for large-scale productions.
- Material Efficiency: Die casting minimizes waste material, as the metal is effectively utilized to create the desired part.
The Role of a Die Casting Tool Manufacturer
The role of a die casting tool manufacturer goes far beyond simply providing molds. The efficacy of the die casting process heavily relies on the expertise and experience of the manufacturer in the following areas:
1. Design and Engineering
To create an effective die, rigorous design and engineering processes must be followed. This includes:
- Creating detailed CAD models of the parts.
- Conducting simulations to ensure the design can withstand the pressures of casting.
- Considering thermal properties and material behavior during cooling.
2. High-Quality Materials
A reliable die casting tool manufacturer ensures the use of high-grade materials for mold construction. This mitigates wear and tear, extends the lifespan of the die, and ultimately contributes to the quality of the cast parts.
3. Precision Manufacturing
Using advanced machining technologies, a reputable tool manufacturer like DeepMould ensures that all die components are produced with meticulous precision, critical for maintaining tight tolerances and achieving the best final product quality.
4. Testing and Quality Assurance
After the die is manufactured, thorough testing is conducted to verify its performance. This includes:
- Prototype casting to determine the effectiveness and accuracy of the design.
- Quality control checks to ensure all specifications are met.
- Adjustments and refinements based on testing results.
5. Continuous Improvement
A leading die casting tool manufacturer invests in continuous improvement practices. They analyze production data, gain feedback from clients, and adopt the latest technologies to enhance their manufacturing processes.
Choosing the Right Die Casting Tool Manufacturer
Selecting the best die casting tool manufacturer is a critical step that can significantly influence your business’s success. Here are some considerations that should guide your decision:
1. Experience and Expertise
Look for manufacturers with considerable experience in the die casting industry. Their knowledge will contribute to better quality and faster turnaround times.
2. Technology and Capabilities
The right manufacturer should utilize modern technology and equipment to create precise dies. Evaluate their machining capabilities and whether they use innovative approaches such as 3D printing for prototyping.
3. Customization Options
Your parts might require unique features. Ensure the manufacturer can provide flexible solutions tailored to your specific needs.
4. Customer Testimonials and Case Studies
Research reviews and case studies from previous clients to gauge the quality of the manufacturers' output and customer service.
5. Compliance and Certifications
Check if the manufacturer adheres to industry standards and possesses relevant certifications. This is crucial for ensuring high-quality production and operational efficiency.
The Future of Die Casting
As industries evolve, die casting technology is also advancing. Innovations such as:
- Hybrid Casting Techniques: Combining die casting with traditional casting methods for superior results.
- Smart Manufacturing: Involving AI and IoT for predictive maintenance and quality control.
- Environmentally Friendly Practices: Implementing sustainable practices in sourcing and manufacturing processes.
These advancements not only enhance production capabilities but also position businesses that utilize die casting at the forefront of their industries.
Conclusion
In summary, partnering with a skilled die casting tool manufacturer like DeepMould can significantly bolster your production capabilities. With a focus on precision, high-quality materials, and cutting-edge technology, you can ensure that your metal fabricating needs are met with excellence. By understanding the ins and outs of the die casting process and choosing the right manufacturer, your business can thrive in a competitive market.
Get Started Today!
If you are keen to explore how die casting can revolutionize your manufacturing process, contact DeepMould today for a consultation. Our team of experts is ready to assist you in navigating the intricacies of metal fabrication with unmatched professionalism and quality.
© 2023 DeepMould. All rights reserved.