The Importance of Plastic Molding in Modern Business
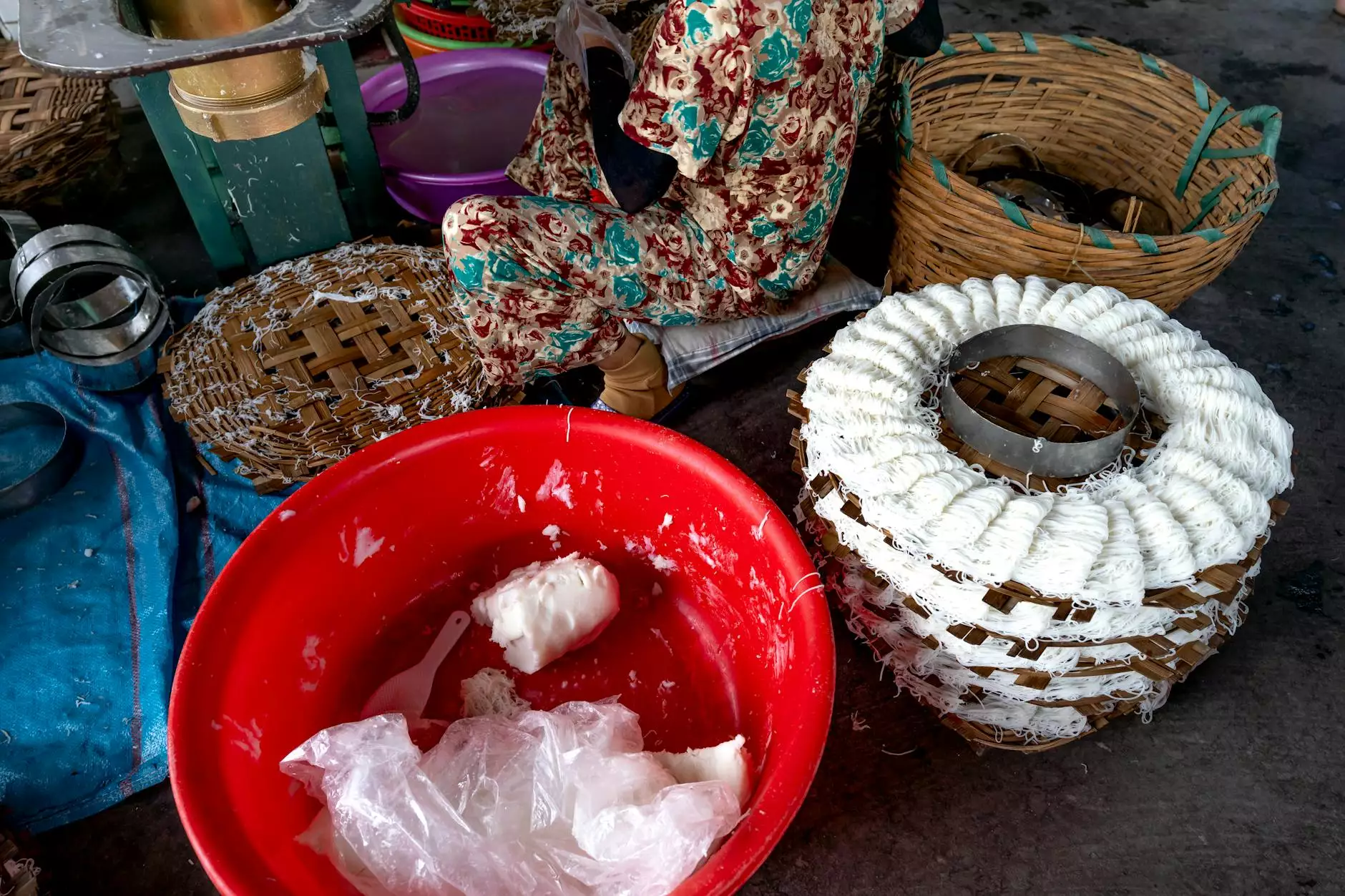
Plastic molding stands as a pivotal technology in today's manufacturing landscape, influencing various industries by enabling the efficient production of high-quality plastic components. From consumer goods to intricate industrial applications, the versatility of plastic molding cannot be understated. This article delves deep into the nuances of plastic molding, its applications, and why it remains indispensable in the fabric of modern business.
What is Plastic Molding?
At its core, plastic molding is a manufacturing process that involves shaping molten plastic into desired forms. This technique is primarily used to create parts and products that are crucial for various applications. The process can take several forms, including:
- Injection Molding: In this technique, molten plastic is injected into a mold to create complex shapes. It's widely used due to its ability to produce large volumes of identical parts with precision.
- Blow Molding: This method is mainly utilized for creating hollow plastic products such as bottles. Air is blown into a heated plastic tube, expanding it to fill the mold.
- Compression Molding: This involves placing a plastic material into an open mold and applying heat and pressure, suitable for larger components.
- Rotational Molding: Ideal for producing large, hollow items. Plastic pellets are placed in a mold, which is then heated and rotated to ensure even coating.
The Versatility of Plastic Molding
Widely Used Across Industries
The applications of plastic molding span across various sectors. Some of the notable industries benefiting from this technology include:
- Automotive: Here, plastic molded components reduce weight, improve fuel efficiency, and cut costs. From dashboards to bumpers, the automotive industry thrives on the benefits of plastic molding.
- Consumer Goods: Everyday products such as containers, toys, and electronics often rely on plastic molding for their durability, design, and affordability.
- Medical Equipment: The precision of injection molding is crucial for producing reliable medical devices, ensuring safety and efficiency in healthcare.
- Packaging: Companies adopt blow molding techniques to produce lightweight, durable packaging solutions that maintain product integrity.
Innovation Through Technology
The evolution of technology has significantly enhanced plastic molding processes. High-precision molds, advanced materials, and automation have improved production efficiency, reduced waste, and increased the scope of design possibilities. Businesses are now able to create intricate designs that were once deemed impossible, leading to innovative products that meet consumer demands.
Why Choose Plastic Molding for Your Business?
With numerous manufacturing techniques available, opting for plastic molding brings several competitive advantages:
1. Cost-Effectiveness
One of the primary benefits of plastic molding is its cost-effectiveness, especially in large-scale production. The ability to produce thousands of identical parts rapidly leads to lower per-unit costs, which is crucial for businesses aiming to maximize profit margins.
2. Design Flexibility
The intricate nature of molds used in plastic molding allows for a variety of designs and specifications. Businesses can collaborate with manufacturers to tailor products to meet specific requirements while retaining aesthetic appeal.
3. Enhanced Durability
Products made through plastic molding are often more durable compared to those made from other materials. This durability translates into longer product lifespans, reducing the need for replacements and contributing to lower waste generation.
4. Environmental Considerations
Modern plastic molding techniques are increasingly utilizing recycled materials and sustainable practices. Companies are adopting eco-friendly approaches to meet consumer demand for sustainable products, giving them a competitive edge in the market.
Focused Applications at Sumiparts.us
At Sumiparts.us, we understand that innovation and quality are essential for businesses in various sectors. Our offerings in machining, laser cut, welding, plastic injection, and vulcanized industrial supplies are tailored to meet the growing demands of our clients. Here’s a closer look at how we integrate plastic molding into our family of services:
Plastic Injection Molding
Our advanced plastic injection molding processes allow us to deliver high-quality, complex plastic parts for numerous applications. By leveraging the latest technology and skilled craftsmanship, we ensure that our clients receive products that meet their exact specifications.
Vulcanized Rubber Applications
Incorporating vulcanized rubber with our plastic molding processes enables us to provide hybrid products that combine the flexibility of rubber with the durability of plastic. This synergy is particularly beneficial in industries where performance under stress and flexibility are essential.
Machining and Laser Cutting Integration
Our machining and laser cutting services complement our plastic molding capabilities. Whether you require custom parts or precision cutting, we work alongside our clients to ensure that all components work seamlessly together, creating a comprehensive solution.
Challenges in Plastic Molding
While plastic molding presents numerous advantages, businesses must also navigate several challenges:
1. Material Choice
Choosing the right type of plastic is crucial. Different plastics have varying properties, and understanding which material best suits the intended application can significantly affect the performance and longevity of the product.
2. Tooling Costs
The initial investment in molds and tools can be substantial. However, this cost amortizes over large production runs, making it essential to evaluate the long-term benefits.
3. Quality Control
Maintaining high-quality standards throughout the production process is imperative. Businesses must implement rigorous quality control measures to avoid defects that could lead to costly recalls.
The Future of Plastic Molding
As technology advances, the future of plastic molding holds promising opportunities. Innovations in materials, the rise of 3D printing technologies, and automation in the manufacturing process will shape the industry landscape. Sustainability will increasingly drive business strategies, with an emphasis on reducing environmental impact.
Conclusion
In conclusion, plastic molding continues to be a cornerstone of modern manufacturing. Its adaptability, efficiency, and cost-effectiveness make it an ideal choice for businesses looking to innovate and thrive. Companies like Sumiparts.us are at the forefront of this evolution, providing exceptional services across multiple disciplines. By understanding the integral role of plastic molding, businesses can make informed decisions that will propel them toward success in a competitive market.
Whether you are in the automotive industry, healthcare, or consumer goods, embracing the advantages of plastic molding will undoubtedly enhance your operational efficiency and product quality. The future is bright for businesses that prioritize innovation, sustainability, and quality in their manufacturing processes.